A factory audit
A factory audit is a one-day procedure. Our specialist visits the factory and checks the constituent documents for compliance with the actual state. If, according to the documents, the factory is located at a certain address, our specialist confirms that the factory is indeed located at the specified address.
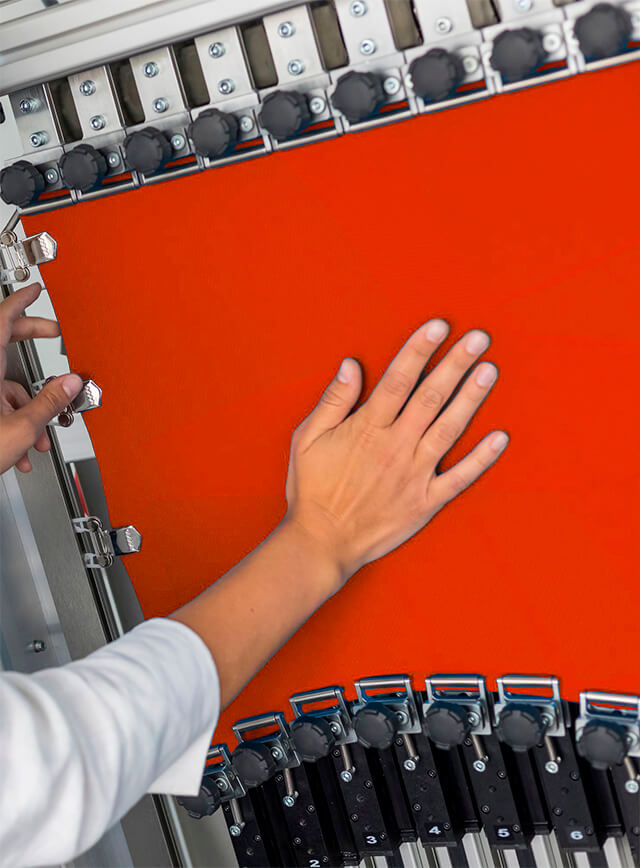